Sterling Impreglon's Brush Plating Technology
What is Brush Plating?
Brush Plating, also known as selective plating, portable electroplating or electroplating on-site, is a specialized surface treatment technique that involves applying a thin layer of metal onto a target area.
Unlike traditional electroplating, which submerges the entire component in a bath of plating solution, Brush Plating is a highly precise method that targets specific areas of the component, making it ideal for localized repairs, enhancements and modifications.
Its humble beginning saw the development from a quick, touch-up for correction of plating defects, to becoming an integral part of the restoration process in many industries.
Application of
Brush Plating
- Corrosion protection.
- Durable repair of worn out or damaged parts.
- Improve wear resistance.
- Galling prevention.
- Anodizing.
- Surface treatments.
- Improve adhesion of surface treatments to selective metals.
- Resizing of mismatched parts.
The Benefits and Advantages of Brush Plating
Brush Plating Vs
Other processes
Superior in many aspects while compared to other forms of repair methods such as Welding, Tank Plating and even Metallizing.
It is a far better choice for cost-effective, localized surface treatments and enhancements.
How Does Brush Plating Works?
Brush plating is an electrolytic process that requires the presence of four crucial elements – Anode, Cathode, Potential and Electrolyte. Each element must be present to ensure a smooth and successful plating process.
The process generally begins with the preparation of the substrate or component, which involves thorough cleaning to ensure it is free from contaminants as well as provide proper masking around the area. The anode also known as a Brush Plating wand, is then used to apply the plating solution directly onto the targeted area. The anode delivers a controlled current to initiate the electrochemical reaction, causing the metal ions in the solution to bond with the substrate, forming a seamless and adherent layer.
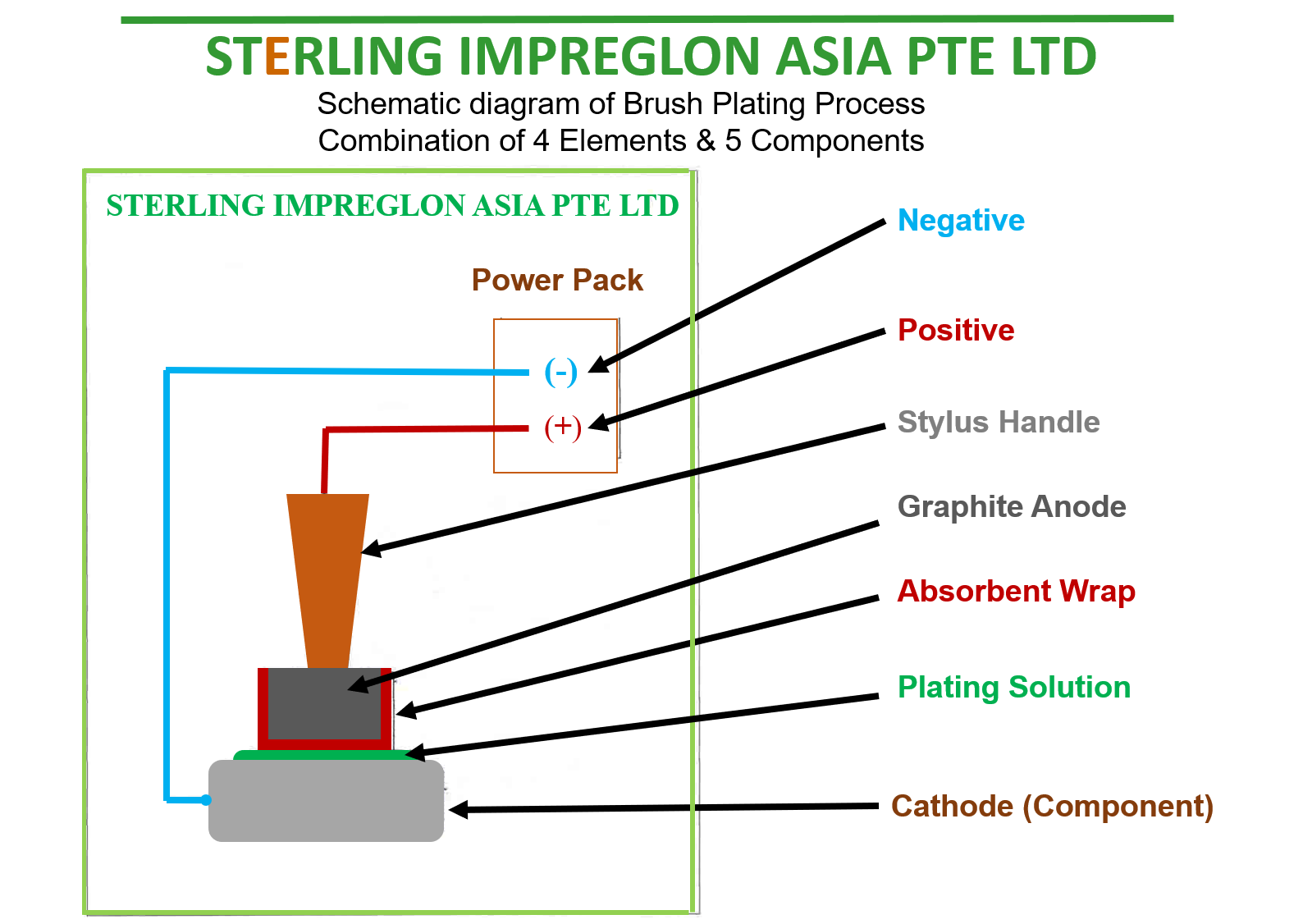